The Advantages of using Drones In Construction
In the world of business, productivity has steadily increased through innovation and adoption of new technology that allows jobs to be done more efficiently with less expense. But construction, today, has been largely unchanged and has lagged behind in adopting technologies that improve productivity. McKinsey reported that the global construction industry, including related spending, accounts for 13% GDP. Unlike other industries that have seen productivity increase at significant rates, construction industry productivity has only increased by 1% per year over the last 20 years. McKinsey identified 7 areas where construction productivity could be increased by 50%-60%. One of them was the introduction of technology and innovation to the construction industry. Drones are an example of a new technology that has the potential to improve project timelines and reduce capital expenditures. We will show you the advantages that drone technology can bring to construction companies.
Drones in Construction – What are the Advantages and How to Use Them
Four major categories can be used to group the advantages of drone surveys for construction companies. Increased efficiency, decreased expenses, improved standards of safety, and improved accuracy in data.
Efficiency of drones in construction
1. Efficiency – Anyone that has manually surveyed a construction site knows it’s not an easy task. Time, a skilled workforce, money and the willingness to redo a survey in case of errors are all required. With traditional methods, five acres can usually be surveyed in an hour. Even novice surveyors can survey 120 acres an hour with drone surveying. This is a 60x increase in efficiency. Traditional surveying would take 24 hours for each 120-acre site. This would be 120 hours per site per year. This would mean 1,200 hours per year of work across all sites.
In comparison, drone surveying can complete each of the annual site surveys within an hour. This means that each site will only take five hours. This would mean that the total time spent to complete all ten surveys is only 50 hours. Drone surveying reduces time spent on a survey site. This increased efficiency has other benefits, too. On a construction site, work is almost always spread across a wide area.
It’s difficult to keep track of everything, and chaos can be the norm for many businesses. In the traditional method of surveying large construction sites, it can take several days to complete. During that time, there is no way to know what changes have occurred since the survey began. It can lead to a re-survey and delay new work. In an ideal world, the numerical differences between drone and traditional surveying would be the same. In an industry like construction, where things don’t always go according to plan, inefficiencies of traditional surveying may compound into further problems down the line. Drone surveying’s increased accuracy, efficiency and adaptability helps construction companies deliver more projects within budget and on time.
Drones in Construction Reduce Expenses
2. Reduced Expenses – As we have already mentioned, the traditional site surveying method requires more time and manpower to complete. These extra hours, surveyors, and equipment will result in higher salaries and other costs associated with construction. Even if you only look at the salaries, and assume that a traditional surveyor earns $100/hour while a drone is paid $120/hour, there can be a substantial savings. Even at the higher hourly rate, the drone surveyor only needs to bill 50 hours per year. This would cost $6,000 in annual fees.
A traditional surveyor, on the other hand, would need 1,200 hours. This 1,200 hours of billable work would cost $2,400 for each survey and $120,000 in total annual fees. Drone surveying can save a small company that needs to perform 50 surveys per year $114,000 in drone surveying costs. These savings will only grow for larger companies, provided that the surveying process goes smoothly and without any need for rework. Different projects could use a variety of assumptions to calculate costs. However, any serious comparison between drone and traditional surveying shows that drones are a much more efficient way to reduce time and expenses.
Improved Safety Standards in Construction Using Drones
3. Improved Safety Standards: Construction is by nature a dangerous business. The surveying process is the same as any other aspect of construction. Surveying traditionally requires that workers enter hard-to-reach places on a site with many moving parts. It’s important to move beyond treating safety as just a check-off item that must be completed to avoid a supervisor’s ire. To improve safety, it is important to change work practices in order to reduce the overall risk workers are exposed.
The way drones are changing the construction industry
The most common use cases can be grouped into five main categories. Site analysis, planning, design, asset inventory and reporting, collaboration and project reporting, and dispute resolution are all possible uses of drones.
Drones are used in different ways by companies in the construction industry. However, they have all improved the project reporting, timelines and inspection processes. This has led to a more reliable, efficient, faster construction operations process. Drones, despite being a relatively young technology, have had a major impact on the construction industry. The expectations around project timelines and surveying have increased significantly. More accurate and accessible data makes communication and dispute resolution between external teams easier.
Drone surveying is one example of how technology can be used to promote and advance environmental sustainability in the construction industry. Worksites that are well-run can lead to fewer mistakes and less waste. The construction process is more eco-friendly, which benefits both the company and the surrounding area. The advantages, of using drone surveying, can help to identify protected areas and address the impact of natural resources.
What you need to implement a drone surveying program
All unmanned aerial vehicles are regulated by the aviation authority. The airspace above your workplace can affect how, when and if you are able to fly.
The FAA is responsible for the commercial drone regulations in the United States. To fly, you need a Part 107 Certificate. Drone operation involves keeping drones in visual line of site, flying under certain altitudes and adhering to specific safety standards while flying over people. The process of obtaining your Part 107 licence is not as difficult as you might think. It requires coursework and an examination. The test is a series of multiple-choice answers covering aviation terminology, weather considerations and the regulations that pilots need to know. The majority of the answers are intuitive.
Don’t worry about how to operate your drone. Flying is easy with apps. It only takes a few moments to set up the flight path of your drone. After that, you can simply press go and watch for any air traffic. Learn how to register your drone, prepare for your flight in the office, conduct your first flight and more by watching our First Flight Video.
Use manual ground control (GCPs), or smart ground control, like AeroPoints, to create a seamless end-to-end solution.
What types of drones are used in construction?
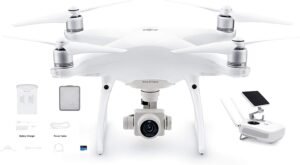
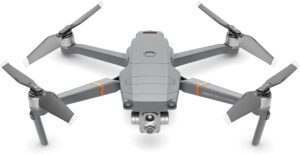
Multirotor drones like DJI’s Mavic 2 Enterprise or the DJI Phantom 4 Advanced have a central frame and multiple rotors. Quadcopters are drones with four rotors. These drones are similar to helicopters, and have vertical takeoff and land capabilities. This makes them easy to maneuver and fly in small spaces.
The Mavic 2 Enterprise comes with a zoom dual camera and thermal imaging. There are multiple camera options available on many fixed-wing drones and /VTOL models. You can choose the one that best matches your resolution requirements.
Drone data can save time and money at all stages of construction projects and for many reasons.